ПАО «Нижнекамскнефтехим». Фото gelio.livejournal.com
Предыдущие статьи:
- Как компании зарабатывают деньги. Производство прямогонного бензина
- Как компании зарабатывают деньги. Производство широкой фракции лёгких углеводородов (ШФЛУ)
- Как компании зарабатывают деньги. Пиролиз и производство этилена
- Как компании зарабатывают деньги. Производство этилбензола
Для получения Бутадиен-стирольного каучука необходим стирол C6H5CH=CH2, который на Нижнекамскнефтехиме создаётся Заводом по производству стирола и полиэфирных смол (СПС). На российских предприятиях производство стирола реализовано по двум принци
пиально разным способам:
– дегидрирование этилбензола C6H5CH2CH3 — как видите, здесь есть пара лишних атомов водорода, если их оторвать, то и получим стирол;
– совместное производство стирола и оксида пропилена CH3CH(O)CH2.
Нижнекамскнефтехим использует оба способа, первый — на установке 1977 года запуска, второй — установка 1982 года. Марка СДЭБ — стирол, полученный каталитически дегидрированием этилбензола.
Марка СДМФК-стирол, полученный в процессе совместного получения стирола и окиси пропилена.
Особенно интересен второй способ, поскольку по этому методу стирол в России больше никто не производит, да и вообще в мире существует только четыре компании, обладающие подобной технологией.
Для реализации второго метода помимо этилбензола требуется пропилен СH3CHCH2 — из него будет образован оксид пропилена. Пропилен на Нижнекамскнефтехиме производится на заводе по производству этилена — его выделяют из продуктов пиролиза.
Два разных продукта получают в одном процессе. Причём ни один из крупнотоннажных продуктов процесса не является побочным — оба целевые и и это делает процесс самым настоящим «два в одном» — просто мечта технолога.
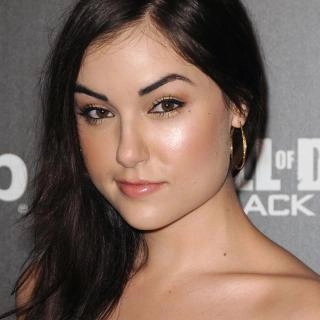
Тут должна была быть глупая шутка про «два в одном»
Первой стадией процесса является окисление этилбензола кислородом воздуха до гидропероксида этилбензола C6H5CH(О2H)CH3. Окисление осуществляют в каскаде реакторов барботажного типа, каждый из которых представляет собой полый аппарат с внутренним змеевиком. Этилбензольную шихту подают в верхнюю часть реактора, воздух – в нижнюю часть реактора.
Получившийся раствор гидропероксида смешивают со свежим молибденовым катализатором, рециркулирующими тяжелыми продуктами со стадии разделения, содержащими катализатор, и с избытком пропилена. Полученную смесь направляют в реакционный узел. При взаимодействии с пропиленом происходит образование оксида пропилена и фенилэтанола C6H5CH(OH)CH3. Реакцию проводят при 100 ÷ 110°С и давлении 25-30 атм, необходимом для поддержания смеси в жидком состоянии.
Продукты реакции (так называемый эпоксидат) направляют в колонну, где отгоняется наиболее летучий пропилен, возвращаемый на взаимодействие с гидропероксидом. Затем в колонне в виде дистиллята получают оксид пропилена, а кубовый остаток перегоняют в вакуумной колонне, отделяя тяжелый остаток, содержащий катализатор. Часть тяжелого остатка возвращают в реакцию, а остальное сжигают или подают на регенерацию катализатора. Дистиллят вакуумной колонны состоит главным образом из этилбензола и фенилэтанола.
Так выглядят колонны ректификации эпоксидата на ПАО «Нижнекамскнефтехим»
Из этой смеси после нейтрализации щелочью вначале отгоняют в колонне наиболее летучий этилбензол, который рециркулируют на синтез гидропероксида. Кубовый остаток колонны поступает в испаритель, где фенилэтанол в токе перегретого водяного пара испаряется и отделяется от смол. Пары, подогретые в теплообменнике до 300 °С, последовательно проходят два реактора, заполненных твёрдым катализатором кислотного типа (активный оксид алюминия), где фенилэтанол подвергается дегидратации (то есть от его молекулы «отрывают» воду). Поскольку реакция дегидратации эндотермична (поглощает тепло), смесь, охладившуюся после первого реактора, подогревают паром в теплообменнике. Суммарная степень превращения фенилэтанола при дегидратации составляет 90%.
Полученные пары охлаждают и конденсируют в холодильнике, после чего водный слой отделяют от органического в сепараторе. Вода вновь идет на получение пара-разбавителя, чем создается система замкнутого водооборота. Органический слой содержит стирол и не превращенный фенилэтанол. Из этой смеси в колонне отгоняют стирол, который дополнительно очищают с получением продукта мономерной чистоты. В кубе колонны остаются остатки фенилэтанола, возвращаемого в процесс.
Михалыч сделал стирол, а Степаныч — оксид пропилена, теперь обсуждают результаты. Фото «Реальное время»
Теперь о цифрах. Мощность ПАО «Нижнекамскнефтехим» по стиролу составляет 270 тыс. тонн/год: по методу дегидрирования этилбензола 130 тыс. тонн/год, по методу совместного получения с оксидом пропилена 140 тыс. тонн/год. Компания является крупнейшим производителем стирола в России. Сейчас в рамках создания нового олефинового комплекса строится ещё одна установка по производству стирола, которая даст ещё около 200 тыс. тонн/год мономера.
Стирол выпускается
промышленностью в виде бесцветной жидкости со слабым специфическим запахом, нерастворимой в воде. В основном стирол используется в качестве сырья для производства полистирола, в том числе вспененного, а также в производстве сополимеров акрилонитрил-бутадиен-стирола и стирол-акрилонитрила, бутадиен-стирольных каучуков, эластичных термопластов и прочих продуктов.
Всего в России производят около 760 тыс. тонн/год стирола. Производители помимо «Нижнекамскнефтехима»: «Газпром Нефтехим Салават» (Газпром), «СИБУР-Химпром» (Сибур), «Пластик» (г. Узловая, Тульская обл.), «Ангарский завод полимеров» (Роснефть). Все из них работают по технологии дегидрирования этилбензола на собственном сырье, кроме «Пластика» — эти этилбензол покупают. В основном стирол перерабатывается на собственных мощностях предприятий. Среди потребителей товарного стирола – «Пеноплэкс»
(полистирол), «Омский каучук» (бутадиен-стирольный каучук).
Около 20% стирола, производимого в России, отправляется на экспорт. Основные потребители: Финляндия, Венгрия, Китай, Казахстан, Турция. В мире производится около 23 млн. тонн/год стирола. Крупнейшие производители — Shell (Великобритания), Lyondell Chemical Company (США, Нидерланды).
Оксид пропилена – один из крупнотоннажных продуктов основного органического и нефтехимического синтеза. Используется в производствах простых полиэфиров, красителей, пропиленгликоля, поверхностно-активных веществ.
В России всего два производителя оксида пропилена — ПАО «Нижнекамскнефтехим» (около 120 тыс. тонн/год) и ООО «Химпром» из г. Кемерово (8 тыс. тонн/год).
Сегодня в мире существуют четыре
крупнейших производителя пропиленоксида — компании Lyondell, Dow, BASF, Shell. Несомненным лидером является компания Lyondell, располагающая суммарными мощностями в объеме около 2 млн тонн/год (с учетом СП). Суммарные мировые мощности по выпуску пропиленоксида достигли порядка 7,1 млн т/год.
вопрос к автору, как к человеку из сферы, в духе нынешней повесточки
а создается ли в рф новая химическая промышленность без участия западных подрядчиков/предоставления технологий
ибо сколько не видел анонсов проектов, везде на ком-то из «недружественных стран» все замкнуто
Есть разные подходы:
— технология по лицензии от компании, так сказать «под ключ», для популярных и распространённых процессов. Здесь наиболее часто лицензиар иностранная компания. Соответственно и оборудование и катализаторы как правило иностранные, но могут быть и местные частично;
— заказ технологии под конкретную задачу. Тут уже проектант (иностранный или российский) и клиент тесно взаимодействуют на предмет того, какое оборудование будет использоваться, поскольку речь идёт не о стандартном процессе;
Дальше скажу по своему опыту — работаю в отрасли органического синтеза, плюс вот изучаю бизнес публичных химических компаний. Если у кого-то другой опыт, пусть делятся своим.
На российских химических предприятиях технологии часто иностранные, но российские тоже есть. Например описанная в статье — разработана в СССР собственными силами.
Оборудование — смотря какое. Емкостное, теплообменное, колонное, насосное, запорные арматуры — практически полностью российского производства. Компрессоры, грануляторы, вращающиеся печи, сложные какие-нибудь клапаны, ещё какая-нибудь чертяйка — чаще иностранные. КИП — примерно пополам.
Катализаторы — есть российские, но все самые крутые современные технологии используют катализаторы, которые оберегаются как «know how» и делаются одной-двумя компаниями в мире.
Системы управления (SCADA) — тут вообще практически олигополия. Во всём мире используют Yokogawa, используют Siemens, а может ещё что-то есть, но я больше не видел.
Силами одной страны сейчас никто в мире не делает современные химико-технологические процессы.
Создать современное сложное химическое производство без привлечения чего-то иностранного, конечно, можно, но это потребует определённого времени и усилий. В принципе вся сегодняшняя российская отрасль каучуков создавалась начиная с 1910-х гг. самостоятельно, поскольку натурального каучука у нас не растёт, потом с Советской Россией никто не хотел иметь дел, пришлось изобретать синтетический каучук и технологию его производства.
Бог Вычислений, и тут интересен опыт Ирана, где нефтехимия одна из основных сфер экспорта, как там живут
А в целом очень интересный цикл у Вас, с большим интересом читаю каждый пост, всё сохраняю и стараюсь хоть немножко разобраться. Спасибо Вам большое!
Сырьё российское (нефтепродукты в данном случае).
С катализаторами сложнее, но плюс в том, что катализаторов нужно не так много и меняют их как правило не часто, раз в три-семь лет (зависит от процесса), можно извернуться и купить через третьи руки, если они для нас забанены, а для ряда процессов так вообще российские есть.
Продавать — всем вроде как по-прежнему нужны автомобильные шины, даже если европейцам они вдруг будут не нужны из нашего каучука (а речь про это пока что не идёт). Северная Америка + Европа — 46,1% поставок каучуков НКНХ. Большая доля, отделу продаж придётся поработать, чтобы продукт перенаправить куда-то, если эти ребята откажутся от российского каучука.
Обслуживать любое иностранное оборудование в химической технологии способны и российские работники заводов, они это делают ежедневно со времён первых пятилеток — искусства сварки, резки, точения, фрезерования металла, ремонта проводки и программирования не утрачены в наших широтах, происхождение оборудования тут значения не имеет. Видел колонну итальянскую 70-х годов, там в паспорте написан сварщик с итальянским именем Джузеппе. Я думаю сварщик этот если жив ещё, даже и не знает, что колона его тут рекорды производительности до сих пор выдаёт — с обслуживанием ребята справляются.