Омский нефтеперерабатывающий завод. Фото «Газпром нефть»
Продолжаем изучать путь природного сырья к превращению в товарный продукт Куйбышевазота — Шинный корд. В
прошлой статье я рассмотрел производство прямогонного бензина, на нефтеперерабатывающем заведе компании «Газпром нефть» в Омске. Следующий продукт в цепочке превращений — бензол, делается здесь же, на Омском НПЗ. Бензол как раз и является тем сырьём, которое нужно Куйбышевазоту.
Какой-то профессиональный юмор
Гениальный англичанин Майкл Фарадей открыл бензол в 1825 г. Десятилетиями считалось, что это явно какой-то углеводород (на что исследователям намекала брутто-формула C6H6). Однако структуру бензола всё никак не удавалось выявить. Химики довольно быстро догадались, что она должна быть циклической, потому что такое соотношение количества атомов углерода и водорода в формуле требует наличия хотя бы одного кольца, а кроме того, каких-то двойных углерод-углеродных связей. Попробуйте сами — сколько вариантов структуры C6H6 можно нарисовать? Только соблюдайте правила — каждый углерод имеет четыре связи, водород — одну, а кратные углерод-углеродные связи могут быть только двойными и тройными (ответ: в базе данных Chem Spider находится 31 вещество с формулой C6H6, одно из них — бензол; чисто математически можно изобразить гораздо больше изомеров, но в реальности их не существует, пока что).
Кроме того, химикам требовалось объяснить некоторые странные свойства бензола. К примеру, известно было три — и только три — различных дихлорбензола (производных бензола, где два из атомов водорода заменены на атомы хлора) с разными температурами плавления. То же самое верно и для всех прочих двузамещённых бензолов. Никто не понимал, почему это так.
Верную формулу предложил в 1865 г. немецкий химик Фридрих Август Кекуле — плоский шестичленный углеродный цикл с чередующимися одинарными и двойными связями между углеродами, причём к каждому атому присоединено по одному атому водорода. В 1928 г. ирландка Катлин Лонсдейл, проведя рентгеноструктурный анализ кристаллов бензола, доказала, что все углерод-углеродные связи в нём имеют одну и ту же длину — промежуточную между длиной обычной одинарной и обычной двойной углерод-углеродной связи. Вещества, содержащие подобную кольцевую структуру (бензол не единственный такой) химики называют
ароматическими. На самом деле, большинство ароматики «воняет конюшней», как говорил мой научрук, но так уж повелось.
«Если вещество хорошо пахнет, то его можно назвать
ароматным, по бытовому, а
ароматический -- всё-таки строгий термин в химии, к хорошему запаху отношения не имеет» (Цитата по книге Зозуля, А.А. «Как говорить терминами, чтобы быть похожим на химика» Екатеринбург: Детская литература, 1975)
Краткая история описания структуры бензола
Пока учёные кидались друг в друга различными структурами бензола, промышленники наладили его получение. Вообще существует четыре метода получения бензола:
- Коксование каменного угля. Бензол содержится в мерзкой смоле, остающейся при производстве металлургического кокса. В прошлом основной метод, но сегодня таким образом получают не более 10% бензола (в России — около 17%).
- Каталитический риформинг прямогонного бензина — примерно 50% выпускаемого бензола. Таким образом бензол получают на Омском НПЗ.
- Пиролиз бензиновых и тяжёлых фракций нефти — примерно 40% выпускаемого бензола. Процесс имеет целью получение олефинов (этилена, пропилена, и т.д.), бензол и другая ароматика получается как побочный продукт.
- Тримеризация ацетилена. Ацетилен — газ, с которым школьники сталкиваются когда бросают карбид кальция в воду. Если взять ацетилен и подвергнуть нагреванию под давлением, его молекулы склеются в бензол. Метод имеет скорее теоретическое значение, чем практическое, промышленных установок нет.
Итак, рассмотрим каталитический риформинг, посмотрим на фотки Омского НПЗ и может быть чьи-то ещё.
Комплекс по производству ароматических углеводородов на Омском НПЗ. Фото «Газпром нефть»
До недавнего времени каталитический риформинг имел своей основной целью повышение октанового числа бензинов. Из всех углеводородов бензиновых фракций самым высоким
октановым числом обладают ароматические углеводороды: бензол (108), толуол (102), этилбензол (98), ксилолы (100), триметилбензол (114) и т.д. Ароматические углеводороды нефти сосредоточены в бензиновой фракции 80–180 °С, но их содержание невелико (около 10% масс), и поэтому октановое число прямогонного бензина не превышает 55 единиц. С целью повышения октанового числа эту фракцию необходимо подвергнуть риформингу – процессу превращения парафиновых углеводородов (т.е. углеводородов с линейной углеродной цепочкой) в ароматические. В результате получается риформат – бензиновая фракция с октановым числом до 100 единиц – ценный высокооктановый компонент товарных бензинов. Но риформаты имеют существенный недостаток – низкое содержание водорода в молекулах углеводородов, а значит, плохую теплотворную способность и высокую склонность к нагарообразованию. При сгорании таких углеводородов выделяется повышенное количество углекислого газа, а при сгорании бензола – бензапирен – один из самых страшных канцерогенов (по этой причине содержание бензола в товарных бензинах ограничивают 1,0% масс, а риформингу подвергают углеводороды, содержащие более 7 атомов углерода, которые переходят в толуол, ксилолы и более высокомолекулярные ароматические углеводороды, то есть не образуют бензол). Другой вариант -- выделять из риформатов бензолсодержащие фракции и продавать бензол как сырьё для нефтехимических предприятий — как раз наш случай.
Современные требования к бензинам ограничивают общее содержание ароматических углеводородов 35% масс. (Евро-4 и Евро-5), а это значит, что в дальнейшем установки риформинга будут строить только для получения индивидуальных ароматических углеводородов – ценнейшего сырья для производства моющих средств, пластмасс, лекарственных препаратов и другой химической продукции. А октановое число
бензинов будут повышать другими методами, не имеющими недостатков, присущих ароматическим углеводородам.
Процессы риформирования проходят при высокой температуре на платино-рениевых катализаторах. Катализаторы представляют собой пористые сферические гранулы диаметром 1,5–2,0 мм, изготовленные из оксида алюминия с напылением платины и рения.
Процесс риформинга проходит в несколько стадий при температурах до 495 °С. Чем выше пределы выкипания фракции (например, не 180, а 200 °С), тем больше получается в итоге целевого риформата. Но с повышением пределов выкипания в сырьевой фракции растет содержание серы, которая отравляет катализатор и быстро выводит его из строя. Для снижения содержания серы в сырье перед установками риформинга устанавливают блок гидроочистки, на котором содержание серы в сырье снижают до 0,0001% масс. Там от серосодержащих соединений «отрывают» сероводород, который отправляется на установку Клаус, о принципе её работы я рассказывал в статье «Производство серы».
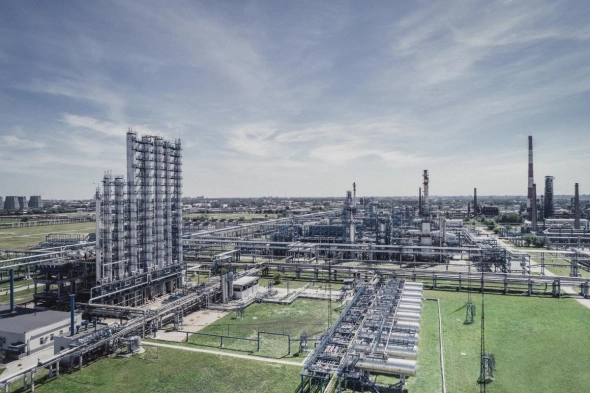
Панорама установки гидроочистки Омского НПЗ. Фото «Газпром нефть»
Побочным положительным фактором процесса риформинга яв
ляется получение значительного количества водорода, выделяемого из молекул углеводородов при их дегидроциклизации. В прежние годы именно установки риформинга были основными источниками водо
рода на НПЗ. Сегодня водород высокого качества получают путем конверсии метана и дальнейшей короткоцикловой концентрацией водорода до 99,9% чистоты. Но водород, получаемый на установках риформинга как побочный продукт, является более дешевым.
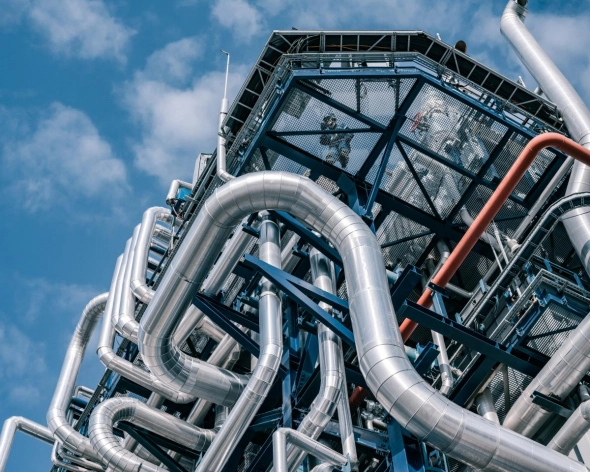
Установка получения водорода на Омском НПЗ. Фото «Газпром нефть»
Повышение давления в системе установки риформинга способствует более длительной работе катализатора. Снижение давления позволяет увеличивать выход риформатов и водорода в процессе риформинга. Повышение температуры процесса приводит к уменьшению выхода риформата, но повышает его октановое число. Кроме того, повышение температуры ведет к быстрому закоксовыванию катализатора. Поскольку катализатор в реакторе находится в неподвижном состоянии, его периодически регенерируют, подавая в систему воздух. При этом кокс выжигается и удаляется из системы в виде углекислого газа.
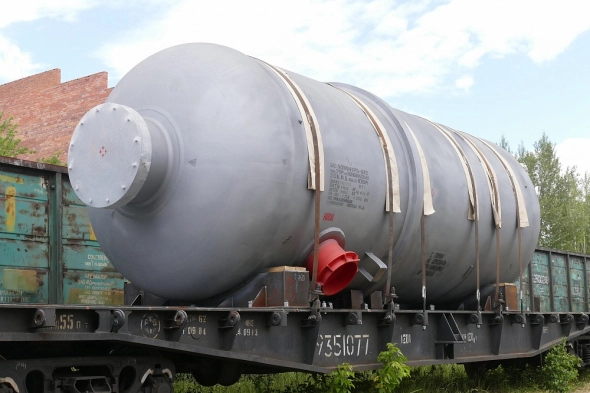
Мужики из АО «Уралхиммаш» сделали для Омского НПЗ вот такие реакторы каталитического риформинга. Фото Уралхимммаш
Поскольку риформаты содержат до 70% масс ароматических
углеводородов, а общее их содержание в товарных бензинах ограничено 35% масс, в состав товарных бензинов риформаты вовлекают в количестве не более 40% масс. Но даже это количество позволяет получать очень высокие октановые числа товарных бензинов.
Выделение ароматики из риформата осуществляют при помощи экстракции. Риформат перемешивают с растворителем, в котором бензол растворяется лучше, чем в риформате, в качестве растворителя выступает сульфолан. Процесс ведут в колонне, похожей на ректификационную. Полученный раствор (экстракт) подвергают ректификационному разделению на ароматику и исходный растворитель, который возвращают на экстракцию. Ароматическая фракция подвергается разделению на бензол, толуол и некоторые другие соединения.
Товарная лаборатория Омского НПЗ. Фото «Газпром нефть»
Теперь о цифрах. Установки риформинга широко распространены в нашей стра
не – их суммарная мощность по сырью превышает 30 млн тонн/год. На Омском НПЗ мощность комплекса по производству ароматических углеводородов составляет 2,4 млн. тонн/год по сырью, производство товарного бензола — оценочно 100 тыс. тонн/год. Суммарно в России производится около 1,5 млн. тонн/год бензола. Другими российскими производителями бензола из нефтяного сырья являются Нижнекамскнефтехим (крупнейший производитель, около 200 тыс. тонн/год), Газпром нефтехим Салават, Уфанефтехим (Башнефть), Славнефть ЯНОС (СП Газпром нефть и Роснефть), Пермьнефтеоргсинтез и Ставролен (Лукойл), Рязанская НПК и Ангарский завод полимеров (Роснефть), Киришинефтеоргсинтез (Сургутнефтегаз), Сибур-Нефтехим, Уралоргсинтез. Производители каменноугольного бензола — НЛМК, Северсталь, Мечел, Западно-Сибирский металлургический комбинат (Evraz), ММК, ПАО «Кокс» (Кемерово) и «Уральская сталь» (Металлоинвест). Суммарная производительность по каменноугольному бензолу в России — 283 тыс. тонн/год.
На экспорт Россия отправляет только 2-8% производимого бензола: в Белоруссию, ЕС и Великобританию, большая же часть потребляется внутри страны. Мировая производительность по продукту около 45 млн. тонн/год.
В сентябре 2021 года средние цены производителей на бензол составили 63559,6 руб/т, в начале года — от 52000 руб/т до 61000 руб/т. Цену на мировом рынке можно отслеживать по фьючерсу на Сингапурской бирже BZF1! (поставка FOB Корея) — цена контракта сейчас составляет 966,38 $/т.
В 1 т. нефти содержится ~20% фракции с температурой кипения до 180 °С (нафты), т. е. 200 кг нафты
В риформатах содержится ~10% бензола, т.е. из 200 кг нафты получим 20 кг бензола.
Это базово. Однако надо понимать, что если целью является получение бензола, то его выход из тонны нефти можно повысить за счёт конверсии толуола, содержащегося в риформате (ещё ~20 кг).
Если в треде есть нефтепереработчики, пусть меня поправят реальными данными